職務経歴
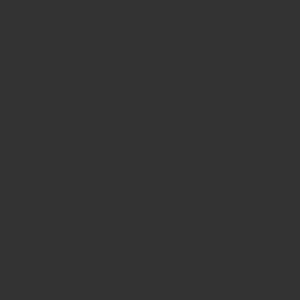
私の職務経歴を書きたいと思います。
社会に出てから2002年、39歳までの16年間は主に製品の設計を行い、それ以降2021年までの19年間はシステムを使った業務改善を行ってきました。
その経緯を時系列で書きたいと思います。
社会に出てからずっと設計、製造畑を歩んで来ました。
少しでもこの経験が皆様のお役に立てればと思います。
- 1 1986年(23歳) オーディオ機器メーカーに就職
- 2 1997年(34歳) 電話交換機のメーカーに1回目の転職
- 3 1998年(35歳) 医療機器のメーカーに2回目の転職
- 4 2002年(39歳) 製品設計から設計管理業務に業務変更
- 5 2003年(40歳) 部品表の電子化
- 6 2004年(41歳) 電気CAD管理システム導入
- 7 2005年(42歳) メカ設計3次元CAD及び管理システム導入
- 8 2007年(44歳) PDM(Product Data Management)導入
- 9 2010年(47歳) 電気CAD管理システムバージョンアップ
- 10 2012年(49歳) PDM導入
- 11 2013年(50歳) 工場から本社に異動
- 12 2018年(55歳) PLM導入【図面管理機能実現】
- 13 2019年(56歳) PLM導入【文書管理機能実現】
- 14 2021年(58歳) MES導入
1986年(23歳) オーディオ機器メーカーに就職
大学を卒業し、オーディオ機器メーカーに就職しました。
オーディオ機器メーカーでは主に業務用製品のマイコンの設計を担当し、年1~2製品のペースでマイコン設計を行いました。
ここで、プログラム言語(C言語)を覚えることができました。
プログラムをする際にパソコンを使うことになり、NEC9801や当時まだDOS/Vと言われていたOSを実装したPC/AT互換機を使うことになります。
そこからパソコンの自作などにも興味を持ち、自宅では自作のPCやノートパソコンなど複数のパソコンを持つようになりました。
パソコンオタクと言われかねませんが、本人は至って普通と思っていました。
今考えると夜中までパソコンをいじっていましたからね。
立派なオタクだったかもしれません(笑)
以後、この知識がベースとなってIT関連の知識を身に着ける事になる。
オーディオメーカーには11年勤務し、当時会社が不景気となり、将来に不安を感じて34歳で退職。
1997年(34歳) 電話交換機のメーカーに1回目の転職
転職活動をした結果、電話交換機のメーカーに就職することができました。
部署は設計となり、ここでもマイコンの設計担当となりました。
しかし、この会社の仕事はかなりの激務で、毎日帰りは午前0時超え。
休日も出勤して、休みは月に数日。
残業代がもらえないブラック企業ではなかったのですが、月の残業が100時間を超えるというとんでもない状態でした。
前の会社も残業は多かったですが、さすがにここまでひどくは無かった。
とてもこのままこの仕事はできないと判断し、1年で退職しました。
その後この会社はグループ内で統廃合され無くなってしまったので、今思うと退職して正解でした。
1998年(35歳) 医療機器のメーカーに2回目の転職
ついに、2回めの転職。
転職グセがつくのではないかと自分自身で不安になりながら転職活動をしました。
マイコン設計のスキルを認めてもらい、医療機器のメーカーの工場に就職することができました。
そこは工場ですが工場内に設計もあり、製品の生産設計だけではなく、本社と協業しながら新製品の設計なども行っていました。
私は新製品の設計をする部署に配属となり、1~2年に1製品のペースでマイコンの設計を行いました。
2002年(39歳) 製品設計から設計管理業務に業務変更
製品設計から設計管理業務に仕事が変わりました。
設計管理業務とは、設計者の業務を支援するもので、具体的には図面や文書など設計者が作成した成果物の管理や、設計者が使用するパソコンやCADなどのインフラの整備をする業務です。
業務改善として、紙管理されていた情報の電子化や、文書を管理するシステムの導入などをリーダーとして推進しました。
この後は、これらの業務改善、システム導入でどのような事を行ったかを説明します。
2003年(40歳) 部品表の電子化
設計、製造で使用する紙の部品表をAccessを使って電子化しました。
私の会社は当時部品表は紙でした。
紙の部品表を電子化することによって、部品表作成の工数削減、部品の検索、閲覧性の向上を狙いました。
電子化は社内だけではなく、社外の業者にも依頼して電子化を行いました。
部品表の電子化は、電気用の部品表とメカ用の部品表をステップを分けて実施し、この段階では電気用部品表の電子化を完了しました。
本社を含め、グループの工場の中で、最初に部品表の電子化を実現したのが私の工場です。
2004年(41歳) 電気CAD管理システム導入
会社では電気の回路図を作成するために電気CADを使用していました。
当時は設計者が電気CADで作成した回路図を個人でローカル管理していたため、訂番管理、変更管理などに多くの工数がかかっていました。
そこで、これらの管理工数の削減、管理品質の向上を目的に電気CADの管理システムを導入しました。
2005年(42歳) メカ設計3次元CAD及び管理システム導入
会社ではメカ設計CADとして、国内メーカーの2次元CADを使用していました。
しかし、メカ設計CADとして、3次元CAD化を推進することになり、3次元CADを導入することになりました。
3次元CADの導入に合わせて、それを管理する管理システムを導入しました。
2007年(44歳) PDM(Product Data Management)導入
工場独自の取り組みとして、設計で使用する紙文書を電子化し、管理する取組を実施しました。
文書管理システムとして、PDMを導入。
医療機器製造に於いて、文書を電子化して管理するためには様々な規制があるため、本システム導入では文書の作成、管理はPDMを使用しましたが、最終的な文書の承認は文書を紙に印刷し、紙に印を押す形で行いました。
それでも今までの紙文書が電子化されることにより、文書作成工数の削減、情報の検索性の向上など大きな効果を上げることができました。
本社及び工場の中で私の工場が初めてPDMを導入しました。
2010年(47歳) 電気CAD管理システムバージョンアップ
2004年に電気CAD管理システムを導入しましたが、導入したシステムのバージョンが保守期限切れとなり、新しいバージョンの電気CAD管理システムに入れ替えることになりました。
新バージョンの電気CAD管理システムの導入では、電気の部品情報だけではなく、メカの部品情報も入力しE-BOM(Engineering-BOM)を作ることができました。
メカ部品の情報の入力は、電気CAD管理システムとメカCAD管理システムを連携するのではなく、メカ設計者が電気CAD管理システムに手入力する形ではありましたが、製品の部品情報が一式入ったE-BOMを初めて作ることができました。
これによって、E-BOMを使った部品の変更管理や、部品情報を工場の他のシステムと共有するなどができるようになりました。
2012年(49歳) PDM導入
工場独自の取り組みとして、2007年に海外製PDMを導入しましたが、導入したバージョンが保守切れとなりバージョンアップが必要となりました。
これを機に、医療機器製造に於ける規格規制に対応して文書を電子化して管理することを決意しました。
医療機器製造に於ける規格規制の一番は米国FDA 21 CFR Part11対応であり、そのためにはシステム導入時にCSV(Computerized System Validation)を実施しなければなりません。
私はCSVの知識を身に着け、会社の標準をつくり、ベンダーと協業しながら新PDMの導入を行いました。
結果システムによる文書の承認ワークフローを導入。
グループで初めて工場にER/ES(Electronic Record/Electronic Signature)に対応したシステムを導入しました。
2013年(50歳) 工場から本社に異動
工場でのシステム導入の経験が認められ、本社に異動し本社とグループ工場が使用する全社システムを導入することになりました。
まずはじめに、当時社内の図面を管理していたシステムの保守が切れるため、新システムを導入することになりました。
私はそのプロジェクトのリーダーとなり、システムの導入を推進しました。
2018年(55歳) PLM導入【図面管理機能実現】
当初図面とE-BOMを管理するシステムの導入を目指しましたが、その後会社の方針で、同じシステムで文書も管理することになりました。
それによってシステムはPLM(Products Life-cycle Management)を使用することになりました。
社内の導入体制も一つのグループの活動から、専任の部が発足し体制が強化されました。
私が工場から異動して5年の時間を費やして、やっと全社システムとしてPLMが導入されました。
この時のPLM導入では、全社で使用する図面とE-BOMの管理が実現されました。
図面、E-BOMはワークフローを使ってレビュー、承認され、ER/ESを実現しました。
このシステム導入が私にとって会社生活最大規模のシステム導入であり、多くの社員、ベンダの協力を得て実現できました。
2019年(56歳) PLM導入【文書管理機能実現】
本プロジェクトでは、図面管理で導入したPLMの文書管理機能を使って、紙の文書を電子化し登録すすることによって、業務効率の向上、電子データの活用を実現しました。
2007年に私は工場でPDMを導入し、文書管理システムによる文書管理を実現しましたが、本システム導入では、導入の対象が本社及び4工場の文書管理となり、文書の種類も莫大に増えました。
また、本社と工場で文書の作成、管理方法もバラバラだったため、それらの業務の標準化も実現しました。
他にもPLMのECR(Engineering Change Request)/ECO(Engineering Change Order)機能を使って複雑な医療の設計変更管理業務をシステム化するするなど、業務効率を飛躍的に向上させることができました。
2021年(58歳) MES導入
私の部署では、別プロジェクトで工場の製造ラインにMES(Manufacturing Execution System)を導入していました。
2019年末、工場導入の直前に新型コロナが蔓延、その影響でシステム導入が延期されました。
延期されたプロジェクトの後任リーダーに私がなり、引き継いでプロジェクトを推進することになりました。
私がリーダーとなった段階で、プロジェクトの状況を確認したところ、導入課題がまだ解決していないことが発覚。
また、システムの仕様も業務の標準化をしない前提で決定していたため、工場個別最適のシステムとなっており、変更が必要なことが分かりました。
そこで私が課題解決の体制を作り、仕様の再調整を行い、プロジェクトの挽回を図りました。
その結果、予定から約1年遅れで工場にMESを導入することができました。